Common Equipment Breakdowns and How to Avoid Them
.png)
Equipment breakdowns can create serious headaches for businesses, leading to unexpected costs and lost productivity. Understanding how to prevent these failures is key to maintaining smooth operations. In this article, we'll explore common equipment breakdowns and how to avoid them, so you can keep your machinery running without a hitch.
Key Takeaways
- Regular maintenance is crucial to avoid breakdowns.
- Operator training can significantly reduce human errors.
- Using technology helps predict and prevent failures.
- Aging equipment often leads to unexpected downtime.
- Creating a safety culture can enhance equipment reliability.
Understanding Equipment Breakdowns
Definition of Equipment Failure
Equipment failure happens when a machine or asset doesn't work as it should. It means something is broken, plain and simple. These unexpected failures can really mess with production schedules, make customers unhappy, and hurt product quality. It's more than just a machine not working; it's a domino effect.
Common Types of Equipment Failures
Equipment failures come in all shapes and sizes. You've got mechanical failures, where moving parts break down or wear out. Then there are electrical failures, like shorts, power surges, or faulty wiring. Don't forget about hydraulic and pneumatic failures, which involve issues with fluid or air pressure systems. And let's not overlook software or control system failures, which can cause a whole host of problems. Understanding these different types is the first step in preventing equipment breakdowns.
Impact of Breakdowns on Operations
Equipment breakdowns can seriously hurt a business. Think about it: production grinds to a halt, deadlines get missed, and customers get annoyed. Plus, there are the costs of repairs, replacement parts, and lost productivity. It's not just about the money, though. Breakdowns can also create safety hazards and damage a company's reputation. It's a big deal, and it's something every business needs to take seriously.
When equipment fails, it's not just about the immediate problem. It's about the ripple effect it has on everything else. It can affect employee morale, customer relationships, and the overall bottom line. That's why it's so important to have a plan in place to deal with breakdowns when they happen.
Key Causes of Equipment Failures
Aging Equipment
Aging equipment is a primary culprit behind many equipment failures. It's just a fact of life that things wear out. As equipment gets older, its components naturally deteriorate. This leads to more frequent repairs and increased downtime. Think about it: older machines need more attention, and finding replacement parts can become a real headache. Plus, the older something is, the harder it is to get the exact part you need. Sometimes, it makes sense to just let old equipment run to failure and invest in something new.
Operator Error
Operator error is another big reason why equipment breaks down. Sometimes, it's just human error – people make mistakes. Maybe they're tired, not properly trained, or just having a bad day. Whatever the reason, mistakes happen, and they can lead to serious equipment damage. It's important to have clear standard operating procedures and provide adequate training to minimize these errors.
- Lack of proper training
- Fatigue
- Inexperience
Lack of Preventive Maintenance
Skipping out on preventive maintenance is like ignoring a ticking time bomb. Regular maintenance, like inspections, lubrication, and timely replacements, keeps things running smoothly. When you neglect maintenance, small problems turn into big ones, leading to unexpected breakdowns and costly repairs. It's way better to catch a problem early than to deal with a full-blown crisis later.
Neglecting preventive maintenance can lead to a cascade of problems. Small issues become major failures, resulting in downtime, lost productivity, and increased repair costs. A proactive approach to maintenance is essential for long-term equipment reliability.
Over-Maintenance
Believe it or not, you can actually overdo it with maintenance. Too much tinkering can be just as bad as not enough. Over-greasing, incorrect adjustments, or unnecessary replacements can cause damage and lead to equipment failure. It's all about finding the right balance. You need to follow the manufacturer's recommendations and avoid unnecessary maintenance that could do more harm than good.
Preventive Maintenance Strategies
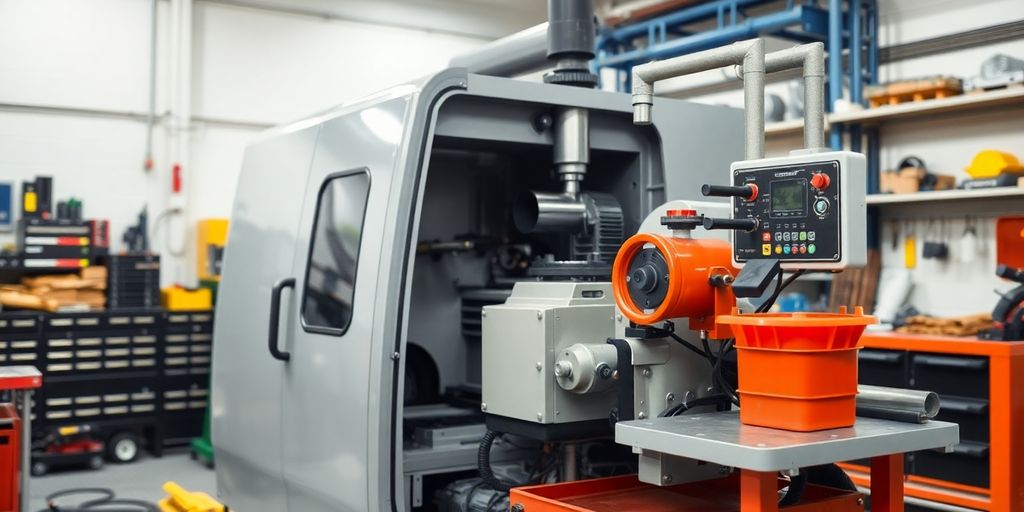
Preventive maintenance is all about stopping problems before they even start. It's like going to the doctor for a check-up – you might feel fine, but they can catch things you wouldn't notice yourself. When it comes to equipment, this means setting up a system to keep everything running smoothly. Let's look at some ways to do that.
Establishing a Maintenance Schedule
First things first, you need a plan. A solid maintenance schedule is the backbone of any good preventive program. This isn't just about fixing things when they break; it's about preventing the breaks in the first place. Think of it like this: you wouldn't drive your car for years without changing the oil, right? Same goes for your equipment. A well-defined schedule ensures that every piece of machinery gets the attention it needs, when it needs it. This includes regular inspections, lubrication, cleaning, and parts replacement. It's about being proactive, not reactive. You can use CMMS software to help with scheduling.
Training and Certification for Operators
Your operators are the people who use the equipment every day, so they need to know what they're doing. Proper training is key to preventing operator error, which is a surprisingly common cause of breakdowns. Make sure everyone knows how to use the equipment correctly, how to spot potential problems, and what to do if something goes wrong. Certification programs can help ensure that your operators have the skills and knowledge they need. It's an investment that pays off in the long run.
Utilizing Technology for Maintenance
We live in a digital world, so why not use technology to your advantage? There are all sorts of tools out there that can help you with preventive maintenance. For example, you can use sensors to monitor equipment performance in real-time, or use software to track maintenance schedules and manage work orders. Technology can help you identify potential problems early on, so you can fix them before they cause a breakdown. It's about working smarter, not harder.
Preventive maintenance is not just a cost; it's an investment. By taking the time to properly maintain your equipment, you can reduce downtime, extend the life of your machinery, and improve your bottom line. It's a win-win situation.
Here are some benefits of a good preventive maintenance strategy:
- Reduced downtime
- Extended equipment life
- Improved safety
- Lower maintenance costs
The Role of Technology in Prevention
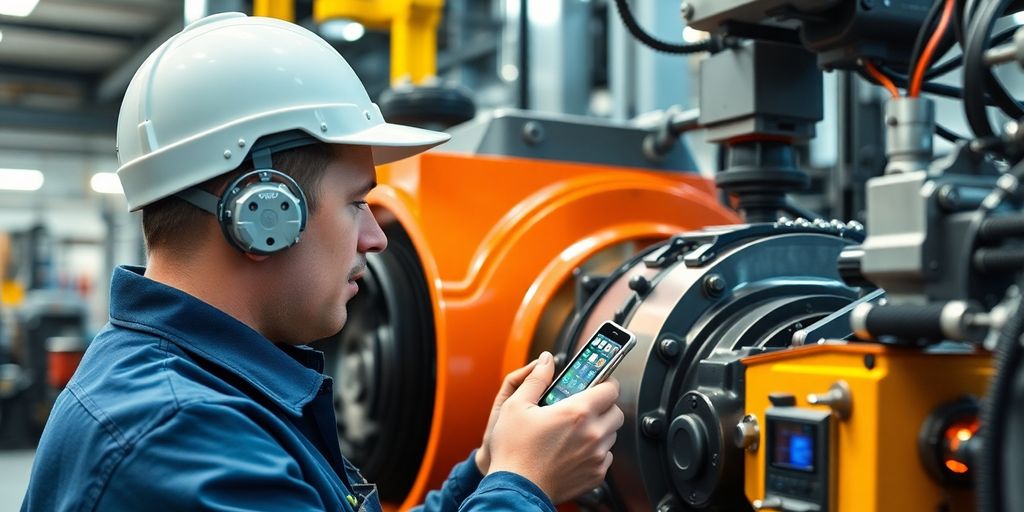
Technology is changing how we handle equipment maintenance. It's not just about fixing things when they break anymore; it's about stopping them from breaking in the first place. Let's look at some ways tech helps with this.
Implementing CMMS Solutions
A CMMS (Computerized Maintenance Management System) is basically software that helps you keep track of all your maintenance stuff. Think of it as a central hub for everything related to keeping your equipment running smoothly. It can schedule maintenance, track inventory, manage work orders, and keep records of everything that's been done. It's a big step up from using spreadsheets or paper.
Predictive Maintenance Techniques
Predictive maintenance is where things get really interesting. Instead of just doing maintenance on a schedule, you use data to figure out when equipment is likely to fail. This could involve sensors that monitor vibration, temperature, or other factors. The idea is to catch problems early, before they cause a breakdown. It's like having a crystal ball for your equipment.
Data Analysis for Equipment Health
All that data from CMMS systems and predictive maintenance tools? It's not much use if you don't analyze it. Data analysis can help you spot trends, identify weak points in your equipment, and figure out the best ways to prevent failures. It's about turning raw data into useful information that can improve your maintenance practices.
Using technology for equipment maintenance isn't just a nice-to-have anymore; it's becoming a necessity. With the right tools and strategies, you can reduce downtime, extend the life of your equipment, and save a lot of money in the long run.
Here's a simple example of how data analysis might work:
- Track the number of hours each piece of equipment operates.
- Monitor the frequency of minor repairs.
- Analyze the relationship between operating hours and repair frequency.
- Adjust maintenance schedules based on the analysis to prevent major failures.
Best Practices for Equipment Management
Regular Inspections and Audits
Regular inspections are super important. Think of it like this: you wouldn't drive your car for years without ever checking the oil, right? Same goes for equipment. Regular visual checks can catch small problems before they turn into big, expensive disasters. Audits, on the other hand, are more in-depth. They're like the annual physical for your machinery, making sure everything is up to snuff. This includes checking for wear and tear, proper function, and adherence to safety standards.
Documentation and Record-Keeping
Okay, I know, paperwork isn't exactly thrilling. But trust me, good documentation can save your bacon. Detailed records of maintenance, repairs, and inspections provide a history of each piece of equipment. This helps you track performance, identify trends, and make informed decisions about when to repair, replace, or upgrade. Plus, it's invaluable for warranty claims and regulatory compliance. Think of it as a health record for your equipment.
Creating a Culture of Safety
Safety isn't just a set of rules; it's a mindset. It's about making sure everyone understands the importance of following procedures, using equipment properly, and reporting potential hazards.
Here are some ways to promote a safety culture:
- Regular safety training sessions
- Open communication channels for reporting concerns
- Incentives for safe behavior
- Management leading by example
A strong safety culture reduces accidents, improves morale, and ultimately boosts productivity. When people feel safe, they're more engaged and focused on their work. It's a win-win for everyone involved.
It's also important to verify equipment ownership when removing items from inventory.
Responding to Equipment Breakdowns
Equipment breakdowns are never fun, but how you handle them can make a huge difference. It's not just about fixing the machine; it's about minimizing downtime, keeping everyone safe, and learning from what happened.
Emergency Response Procedures
First things first: safety. Make sure everyone is safe and the area is secure. This might mean shutting down power, evacuating the area, or using safety barriers. Have a clear, written procedure that everyone knows. This should include:
- Immediate shutdown protocols.
- Emergency contact information.
- First aid procedures.
- Evacuation routes.
Communication During Breakdowns
Communication is key. When something breaks, everyone needs to know what's going on. This includes:
- Notifying supervisors and maintenance teams immediately.
- Keeping operators informed about the status of repairs.
- Communicating any changes to production schedules.
A good communication plan can prevent panic and keep everyone on the same page. It's about transparency and making sure people know what to expect.
Post-Breakdown Analysis
Once the equipment is up and running, don't just move on. Take the time to figure out what caused the breakdown and how to prevent it from happening again. This could involve:
- Inspecting the failed parts.
- Reviewing maintenance records.
- Talking to operators and maintenance staff.
- Updating maintenance procedures.
Long-Term Solutions for Equipment Reliability
Investing in New Equipment
Sometimes, the best long-term solution is simply replacing old equipment. Aging equipment often leads to more frequent breakdowns and higher maintenance costs. While the initial investment can be significant, new equipment usually comes with improved efficiency, better technology, and lower long-term operating expenses. It's a tough decision, balancing the cost of replacement against the ongoing costs of keeping older machines running.
Upgrading Existing Machinery
Upgrading existing machinery can be a cost-effective alternative to full replacement. This might involve installing new control systems, replacing worn components with more durable ones, or adding features that improve performance and reliability. Upgrading can extend the lifespan of your equipment and improve its overall efficiency. It's important to carefully assess whether the upgrade will provide a sufficient return on investment, considering factors like the age of the machine and the availability of upgrade options.
Continuous Improvement Processes
Implementing continuous improvement processes is key to long-term equipment reliability. This involves regularly reviewing maintenance practices, identifying areas for improvement, and implementing changes to optimize performance and reduce downtime. It's not a one-time fix but an ongoing effort to refine processes and adapt to changing conditions. Here are some steps to consider:
- Regularly analyze equipment performance data to identify trends and potential problems.
- Solicit feedback from operators and maintenance personnel to identify areas for improvement.
- Implement changes based on data and feedback, and monitor their effectiveness.
A culture of continuous improvement fosters a proactive approach to equipment management, where problems are identified and addressed before they lead to breakdowns. This approach requires commitment from all levels of the organization, from management to front-line workers.
Wrapping It Up
In the end, dealing with equipment breakdowns is no walk in the park. They can hit your wallet hard and throw a wrench in your daily operations. But here’s the good news: many of these issues are preventable. By keeping up with regular maintenance, training your staff properly, and using the right tools, you can dodge a lot of those headaches. Sure, you might not be able to stop every breakdown from happening, but with a solid plan in place, you can definitely cut down on them. So, take the time to invest in your equipment and your team. It’ll pay off in the long run.
Frequently Asked Questions
What is equipment failure?
Equipment failure happens when a machine or tool stops working properly. This can cause delays and problems in production.
What are the main causes of equipment breakdowns?
The most common causes include old equipment, mistakes made by operators, not doing regular maintenance, and sometimes doing too much maintenance.
How can we prevent equipment failures?
You can prevent failures by keeping a regular maintenance schedule, training operators well, and using technology to help monitor equipment.
What role does technology play in preventing breakdowns?
Technology can help by using software to track maintenance, predict when equipment might fail, and analyze data to keep machines running smoothly.
What should we do if equipment breaks down?
If something breaks, follow emergency procedures, communicate with your team, and analyze what caused the breakdown to prevent it in the future.
How can we improve equipment reliability in the long term?
Investing in new machines, upgrading old ones, and continuously improving maintenance processes can help make equipment more reliable.