How to Create a Maintenance Schedule for Heavy Machinery
.png)
Creating a maintenance schedule for heavy machinery is essential to keep your equipment running smoothly and avoid costly breakdowns. With the right plan in place, you can ensure that your machines are inspected and serviced regularly, which not only extends their lifespan but also boosts productivity. In this article, we’ll walk you through the steps to develop an effective maintenance schedule tailored to your heavy equipment needs.
Key Takeaways
- Understand the importance of regular maintenance to prevent breakdowns.
- Follow manufacturer guidelines to set maintenance intervals for different equipment.
- Incorporate daily inspections and scheduled tasks into your routine.
- Utilize technology like fleet management software to track maintenance activities.
- Train your staff on best practices to foster a culture of maintenance awareness.
Understanding Heavy Equipment Maintenance
Definition and Importance
Heavy equipment maintenance is all the stuff you do to keep your machines running smoothly. It's about preventing breakdowns and keeping your equipment in good shape. Think of it as taking care of your investment. The daily grind of pressure, dust, heat, and constant use wears down parts faster than you can say "construction." That's why understanding the ins and outs of heavy equipment maintenance is crucial.
Regular maintenance extends machine life, reduces repair costs, minimizes downtime, improves productivity, and reduces project delays.
Common Types of Maintenance
There are a few main types of maintenance you should know about:
- Corrective Maintenance: This is when you fix something after it breaks. Think repairs and part replacements.
- Preventative Maintenance: This is all about stopping problems before they happen. Regular inspections and care are key.
- Specialized Maintenance: This is maintenance that's specific to certain types of equipment. For example, concrete pump trucks have unique needs.
Key Components of Maintenance
Effective heavy equipment maintenance involves several key components:
- Regular Inspections: Checking for wear and tear, leaks, and other potential issues.
- Lubrication: Keeping moving parts properly lubricated to reduce friction and wear.
- Fluid Checks: Monitoring and changing fluids like oil, coolant, and hydraulic fluid.
- Component Replacement: Replacing worn or damaged parts before they cause major problems.
- Documentation: Keeping detailed records of all maintenance activities.
Establishing a Maintenance Schedule
Alright, so you know why maintenance is important. Now, how do you actually plan it out? It's not as simple as just picking random dates. A solid maintenance schedule is the backbone of keeping your heavy equipment running smoothly. Let's get into the nitty-gritty.
Identifying Equipment Needs
First things first, you gotta know what each piece of equipment actually needs. This isn't a one-size-fits-all situation. A bulldozer isn't going to have the same requirements as a concrete mixer. Start by looking at the equipment's usage. How many hours a week is it running? What kind of conditions is it operating in? Is it constantly dealing with heavy loads and rough terrain? All of this impacts how often it needs to be checked and serviced. Consider these factors:
- Operating hours per week
- Typical load and stress levels
- Environmental conditions (dust, heat, etc.)
Choosing the right equipment from the start can also help align with your maintenance needs.
Consulting Manufacturer Guidelines
Don't try to reinvent the wheel here. The manufacturer of your equipment knows it best. Always, always, always consult the manufacturer's guidelines. These guidelines will give you a baseline for scheduled maintenance, including recommended service intervals for things like oil changes, filter replacements, and inspections. These manuals are goldmines of information, so dig them out and actually read them. They often include specific instructions and warnings that you won't find anywhere else.
Creating a Custom Schedule
Okay, so you've got the manufacturer's recommendations, and you know how your equipment is being used. Now it's time to create a custom schedule. This is where you tailor the maintenance plan to your specific needs. Take the manufacturer's guidelines and adjust them based on your equipment's actual usage and operating conditions. For example, if you're operating in a particularly dusty environment, you might need to change air filters more frequently than the manufacturer recommends. Preventative planning helps maximize the longevity of your machinery.
Implementing Preventative Maintenance Practices
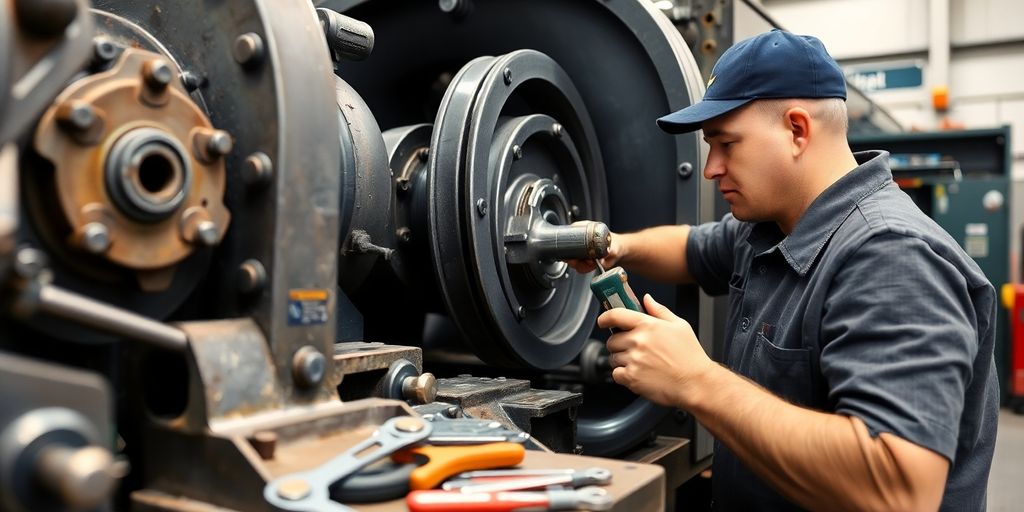
It's easy to fall into the trap of only fixing things when they break, but with heavy machinery, that approach can lead to major headaches and expenses. Implementing preventative maintenance practices is all about being proactive. It's about catching small issues before they turn into big, costly problems. Think of it as regular check-ups for your equipment to keep everything running smoothly.
Daily Inspection Routines
Daily inspections are your first line of defense. These aren't meant to be complicated or time-consuming, but rather a quick once-over to spot anything obvious. It's like a pilot's pre-flight check. Here's what a typical daily inspection might include:
- Check fluid levels: Oil, coolant, hydraulic fluid, and fuel. Top off as needed.
- Inspect for leaks: Look for any signs of drips or puddles under the equipment.
- Check tires: Make sure they're properly inflated and look for any damage.
- Inspect hoses and belts: Look for cracks, fraying, or looseness.
- Test lights and signals: Ensure all lights, signals, and alarms are working properly.
Daily inspections are crucial. They allow operators to identify potential issues early, preventing minor problems from escalating into major repairs. This proactive approach minimizes downtime and extends the lifespan of your equipment.
Scheduled Maintenance Tasks
Scheduled maintenance goes beyond the daily checks. These are more in-depth tasks performed at specific intervals, based on manufacturer recommendations or equipment usage. These tasks might include:
- Oil changes: Regularly changing the oil and filters is essential for engine health.
- Filter replacements: Air, fuel, and hydraulic filters should be replaced according to schedule.
- Lubrication: Grease all moving parts to reduce friction and wear.
- Component inspections: Inspect critical components like brakes, steering, and suspension.
- Fluid analysis: Regularly testing fluids can reveal potential problems before they cause damage.
Utilizing Telematics for Monitoring
Telematics systems are becoming increasingly common in heavy equipment management. These systems use sensors and GPS technology to collect data on equipment performance, location, and usage. This data can be used to:
- Track equipment hours: Monitor usage to schedule maintenance based on actual operating time.
- Monitor fuel consumption: Identify inefficient operation and potential fuel theft.
- Detect fault codes: Receive alerts when the equipment detects a problem.
- Track location: Monitor equipment location for security and utilization purposes.
- Analyze performance: Identify trends and patterns to optimize maintenance schedules. Using telematics and GPS technology can really streamline your maintenance program.
Tracking Maintenance Activities Effectively
It's easy for maintenance to fall through the cracks, especially when you're juggling a lot. But keeping good records is super important. It helps you spot problems early, plan for the future, and make sure you're getting the most out of your equipment. Think of it as giving your machines a voice, telling you what they need to stay healthy.
Using Fleet Management Software
Okay, so spreadsheets can work, but let's be real – they can get messy fast. Fleet management software is where it's at. It's like having a digital assistant dedicated to your equipment. These programs can automatically track usage, schedule maintenance, and even send alerts when something's due. It's a game-changer for staying organized and on top of things.
Documenting Service History
Every repair, every oil change, every little tweak – write it down! This creates a service history for each piece of equipment. This record should include:
- The type of service performed.
- Any parts that were replaced.
- Notes on components that might need replacing soon.
- The date of the next scheduled maintenance.
- Any other issues that were noticed.
This info is invaluable when troubleshooting problems or making decisions about repairs vs. replacement.
Setting Up Alerts and Reminders
Life gets busy, and it's easy to forget about upcoming maintenance. That's where alerts and reminders come in. Set them up in your fleet management software (or even your calendar) to remind you about scheduled tasks. This helps prevent missed deadlines and keeps your equipment running smoothly.
Think of alerts as your equipment's way of tapping you on the shoulder and saying, "Hey, don't forget about me!" They're a simple but effective way to stay proactive and avoid costly breakdowns.
Training Staff for Maintenance Success
It's easy to overlook, but proper training is a game-changer for keeping your heavy machinery in top shape. You can have the best maintenance schedule in the world, but if your team isn't equipped with the right knowledge, it won't matter. Let's get into why training is so important and how to make it work.
Importance of Employee Training
Training isn't just about ticking boxes; it's about empowering your team to be proactive and efficient. Well-trained staff can spot potential problems early, perform routine maintenance tasks correctly, and understand the importance of following procedures. This translates to fewer breakdowns, longer equipment life, and a safer work environment. Plus, when employees understand how their work contributes to the bigger picture, they're more likely to take pride in what they do.
Best Practices for Training
Effective training goes beyond just reading manuals. Here are some best practices to consider:
- Hands-on training: Let employees get their hands dirty. Practical experience is invaluable.
- Regular refreshers: Don't just train once and forget. Provide ongoing training to keep skills sharp and updated.
- Manufacturer guidelines: Always refer to the manufacturer's recommendations for maintenance procedures.
- Mentorship programs: Pair experienced technicians with newer employees for on-the-job learning.
- Use of technology: Incorporate videos, simulations, and online resources to make training more engaging.
Investing in training is an investment in your equipment's longevity and your team's capabilities. It's about creating a culture of continuous improvement and ensuring that everyone is working towards the same goal: keeping your machinery running smoothly.
Creating a Maintenance Culture
Building a maintenance culture means making maintenance a priority at all levels of the organization. It's about fostering a sense of responsibility and ownership among employees. Here's how to do it:
- Lead by example: Show that maintenance is important by actively participating in maintenance activities.
- Recognize and reward good maintenance practices: Acknowledge employees who go above and beyond in their maintenance efforts.
- Encourage open communication: Create a safe space for employees to report problems and suggest improvements.
- Provide the right tools and resources: Make sure employees have the equipment and information they need to do their jobs effectively.
- Regular meetings: Hold regular meetings to discuss maintenance issues and share best practices.
Evaluating Maintenance Effectiveness
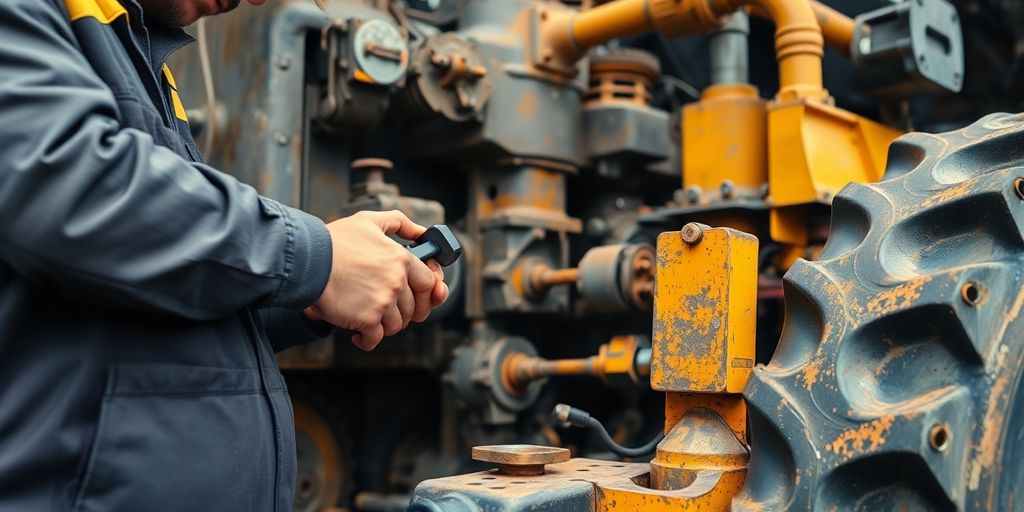
It's not enough to just do the maintenance; you need to know if it's actually working. Are you seeing a reduction in downtime? Are repair costs going down? This section is all about figuring that out.
Analyzing Downtime and Repairs
The first step is to look at the hard numbers. Track how often equipment is out of service and why. Dig into the repair logs. Are certain machines constantly breaking down? Are specific parts failing more than others? This data will tell you where your maintenance efforts are paying off and where they're falling short. For example, you might find that daily preventative maintenance on your excavators has significantly reduced hydraulic failures, but your wheel loaders are still experiencing frequent tire problems. This suggests you need to adjust your maintenance schedule or practices for the loaders.
Gathering Feedback from Operators
Don't just rely on data. Talk to the people who use the equipment every day. Operators often have a good sense of when something isn't quite right, even if it doesn't trigger a formal breakdown. Their insights can help you identify potential problems early and fine-tune your maintenance procedures. Consider implementing a simple feedback system, like a quick checklist they fill out at the end of each shift, or regular meetings to discuss equipment performance. This can help you catch issues before they become major headaches and improve your overall fleet utilization.
Adjusting Schedules Based on Performance
Your maintenance schedule shouldn't be set in stone. It's a living document that needs to be updated based on what you're learning. If you're still experiencing too much downtime or high repair costs, it's time to make some changes. Maybe you need to increase the frequency of certain inspections, switch to a different type of lubricant, or invest in better training for your maintenance staff. The key is to be flexible and willing to experiment until you find a schedule that works for your specific equipment and operating conditions.
Think of your maintenance schedule as a continuous improvement project. Regularly review your data, gather feedback, and make adjustments as needed. The goal is to optimize your maintenance efforts to minimize downtime, reduce costs, and extend the life of your equipment.
Here are some things to consider when adjusting your maintenance schedule:
- Equipment age and condition
- Operating environment
- Manufacturer recommendations
- Operator feedback
- Maintenance budget
Special Considerations for Specialty Equipment
Some equipment needs a little extra TLC. It's not just about the standard maintenance; you've got to think about the specific demands placed on these machines. Let's look at a couple of examples.
Maintenance for Concrete Pump Trucks
Concrete pump trucks are workhorses on construction sites, but they face unique challenges. They're constantly dealing with abrasive materials, which can lead to wear and tear on critical components. Regular inspections are key to keeping these trucks running smoothly.
Here's a quick rundown of what to keep an eye on:
- Hydraulic System: Check the hydraulic oil regularly. Contamination is a big issue, so replace or clean the oil if it's looking dirty. Also, inspect hydraulic hoses for damage and replace them as needed.
- Pipes and Seals: Look for corrosion on steel pipes and check rubber seals for any signs of wear or damage. Replace faulty gaskets on the boom to prevent leaks.
- Electrical Components: Inspect electrical elements for loose connections or damage. Fix any malfunctioning components promptly.
Concrete pump trucks require meticulous attention to detail. Overlooking seemingly minor issues can quickly escalate into major problems, leading to costly downtime and project delays.
Hydrovac Truck Maintenance
Hydrovac trucks use high-pressure water and a powerful vacuum to excavate soil. This process puts a lot of stress on the equipment, so maintenance is crucial. Here are some key areas to focus on:
- Vacuum System: Inspect the vacuum hoses and connections for leaks or damage. Ensure the vacuum pump is functioning correctly and that filters are clean.
- Water System: Check the water pump and nozzles for clogs or wear. Inspect the water tank for leaks or corrosion.
- Debris Tank: Regularly empty and clean the debris tank to prevent buildup and ensure proper operation. Inspect the tank for damage or leaks.
Unique Challenges and Solutions
Specialty equipment often presents unique maintenance challenges that require creative solutions. For example, concrete pump trucks are prone to particle contamination, while hydrovac trucks face the risk of freezing in cold weather. Understanding these challenges and implementing appropriate preventative measures is essential for maximizing equipment uptime. Make sure you're following industry standards for machine tools.
Here's a table summarizing some common challenges and solutions:
| Challenge | Solution the vacuum system, water system, and debris tank. These components are critical for the truck's operation, and neglecting them can lead to breakdowns and costly repairs.
Wrapping It Up
Creating a solid maintenance schedule for your heavy machinery isn't just a good idea—it's a must. It keeps your equipment running smoothly and helps avoid those nasty surprise repairs that can hit your wallet hard. By sticking to a routine and keeping an eye on each machine's needs, you can extend its life and boost productivity. Remember, it’s all about being proactive instead of reactive. So, take the time to set up a plan, train your team, and keep track of everything. In the long run, you’ll save time, money, and a whole lot of headaches.
Frequently Asked Questions
What are the benefits of maintaining heavy machinery?
Keeping heavy machinery well-maintained can help it last longer, reduce repair costs, and keep work running smoothly without delays.
What types of maintenance do heavy machines require?
Heavy machines typically need two main types of maintenance: preventative maintenance, which helps avoid problems, and corrective maintenance, which fixes issues when they arise.
How do I create a maintenance plan for my equipment?
To make a maintenance plan, start by figuring out what each machine needs, follow the manufacturer's guidelines, and then set up a schedule that works for your operations.
How can I track maintenance for my heavy equipment?
You can use fleet management software to track maintenance schedules, usage, and alerts for when maintenance is due, making it easier to stay organized.
Why is employee training important for maintenance?
Training employees helps them understand how to properly care for the machines, which can prevent mistakes and ensure everything runs well.
How can I tell if my maintenance schedule is working?
You can evaluate your maintenance schedule by looking at how often machines break down, getting feedback from operators, and adjusting the schedule based on performance.