How to Extend the Life of Your Heavy Equipment Fleet
.png)
If you're managing a fleet of heavy equipment, you know how crucial it is to keep everything running smoothly. Extending the life of your machines not only saves money but also boosts productivity. So, let's dive into some practical tips on how to extend the life of your heavy equipment fleet. By following these strategies, you can ensure your equipment serves you well for years to come.
Key Takeaways
- Regular maintenance is key to preventing costly breakdowns.
- Training operators reduces the chance of damage from misuse.
- Using technology helps monitor equipment health and predict issues.
- Choosing quality parts for repairs can save money in the long run.
- Proper load management and minimizing idle time extend equipment life.
Understanding Heavy Equipment Lifespan
Factors Influencing Equipment Longevity
Okay, so you want your heavy equipment to last. Makes sense! A bunch of things affect how long your machines stick around. First, think about how often you're using them and how hard you're pushing them. A machine constantly working at its max is gonna wear out faster than one that's used more gently. The environment matters too. Are you in a super dusty area? That'll impact things. What about extreme temperatures? Yep, that too. And of course, how well you maintain your equipment plays a huge role. Neglecting routine upkeep procedures is a surefire way to shorten its lifespan. To avoid costly damage, consider effective drainage solutions for your property, which protect outdoor environments where heavy equipment may operate.
- Usage intensity
- Environmental conditions
- Maintenance practices
Average Lifespan of Common Machines
So, how long should your equipment last? Well, it varies. A well-maintained excavator might give you 10-15 years, while a loader could last a bit longer. But remember, these are just averages. A lot depends on those factors we just talked about. Think about it like this: a car driven gently on highways will last longer than one constantly doing stop-and-go in the city. Same principle applies here. Knowing the average lifespan helps with budgeting and planning for replacements.
Signs of Aging Equipment
How do you know when your equipment is getting old? Keep an eye out for a few key things. Are you seeing more frequent breakdowns? That's a big one. Are parts becoming harder to find? Another red flag. Is the machine's performance just not what it used to be? Time to start thinking about what's next. Don't ignore these signs. Catching them early can help you make informed decisions about repairs or replacements. Ignoring these signs can lead to bigger problems down the road. It's like ignoring that weird noise your car is making – it's probably not going to fix itself. Also, consider the financial aspects of keeping older equipment running. At some point, the cost of repairs will outweigh the value of the machine.
It's important to keep detailed records of all maintenance, repairs, and inspections. This historical data can help you predict future maintenance needs and troubleshoot problems more effectively. Plus, it gives you a clear picture of when it might be time to retire a machine.
Implementing Regular Maintenance Practices
Daily Inspection Checklists
Starting each day with a quick equipment check can save you big time and money down the road. Think of it as a morning health check for your machines. It's about catching the small stuff before it turns into a major breakdown. Make sure your operators have a clear, simple checklist. This should include things like:
- Checking fluid levels (oil, coolant, hydraulic fluid).
- Inspecting hoses and belts for wear and tear.
- Looking for any visible damage or leaks.
- Testing the brakes and lights.
A well-executed daily inspection is the first line of defense against unexpected downtime. It's a small investment of time that yields significant returns in equipment longevity and operational efficiency.
Scheduled Maintenance Plans
Don't just wing it when it comes to maintenance. You need a solid, scheduled maintenance plan. This isn't a one-size-fits-all thing; it needs to be tailored to each piece of equipment, taking into account the manufacturer's recommendations and your specific operating conditions. A good plan will include:
- Regular oil changes and filter replacements.
- Lubrication of moving parts.
- Inspection and adjustment of critical components.
- Scheduled routine maintenance to prevent issues.
Fluid Analysis and Sampling
Think of fluid analysis as a blood test for your equipment. It can tell you a lot about what's going on inside, like detecting early signs of wear or contamination. Regular sampling can help you:
- Identify contaminants like dirt, water, or coolant.
- Detect excessive wear metals, indicating internal component wear.
- Monitor the condition of the fluid itself, ensuring it's still providing adequate protection.
Training Operators for Optimal Performance
It's easy to overlook the impact of operator training, but it's a game-changer for extending the life of your heavy equipment. A well-trained operator is less likely to abuse the machinery, leading to fewer breakdowns and a longer lifespan for your fleet. Let's face it, even seasoned pros can develop bad habits over time.
Importance of Comprehensive Training
Comprehensive training is the bedrock of optimal equipment performance. It's not just about showing someone how to turn the machine on and off. It's about instilling a deep understanding of the equipment's capabilities, limitations, and proper operating procedures. This includes everything from pre-shift inspections to understanding load charts and recognizing potential hazards. Dealership training can keep your staff up-to-date on new technologies and procedures. Proper machine training ensures efficient equipment use, directly impacting machine life. This principle also applies when managing your outdoor space—common landscaping mistakes can reduce project lifespan if not handled by trained professionals.
Best Practices for Equipment Use
Here are some best practices to incorporate into your operator training program:
- Daily Inspections: Operators should conduct thorough pre-shift inspections, checking fluid levels, tire pressure, and all critical systems. A checklist ensures nothing is missed.
- Proper Warm-Up Procedures: Teach operators the importance of warming up the engine before putting it under heavy load. This allows the oil to circulate properly and protects engine components.
- Smooth Operation: Emphasize smooth, controlled movements. Abrupt starts, stops, and turns put unnecessary stress on the equipment.
Training programs should demonstrate the proper way to use your equipment. Improper usage can lead to unintentional damage, so the people operating the machines on a daily basis should have a thorough idea of what they're doing. By minimizing the chance of incidents that could result in machine damage, you can reduce your repair bills and make your equipment last longer.
Reducing Operator Errors
Operator error is a significant contributor to equipment damage and downtime. By addressing common mistakes through targeted training, you can significantly reduce these incidents. Understanding load limits is crucial to avoid over stressing the machine. Here's how:
- Simulators: Use simulators to provide operators with a safe environment to practice operating the equipment and learn how to respond to different situations.
- Mentoring Programs: Pair experienced operators with newer ones to provide on-the-job training and guidance.
- Regular Refresher Courses: Provide regular refresher courses to reinforce best practices and address any emerging issues.
Utilizing Technology for Equipment Monitoring
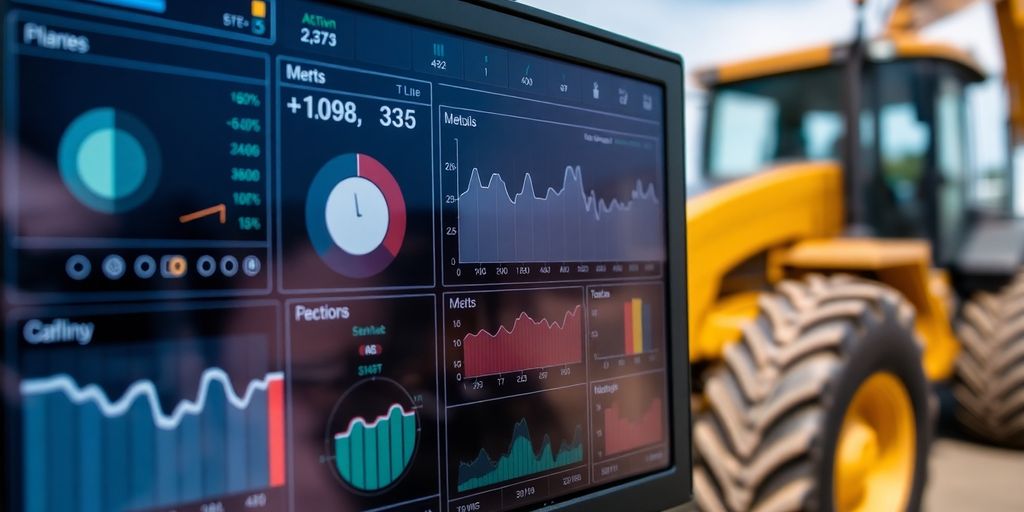
Technology offers some amazing ways to keep tabs on your heavy equipment, helping you catch problems early and extend its lifespan. It's not just about knowing where your equipment is; it's about understanding how it's being used and what kind of stress it's under. Let's look at some specific technologies that can make a real difference.
Telematics and Data Tracking
Telematics systems are a game-changer. They provide a constant stream of data about your equipment's performance, location, and condition. Think of it as a health monitor for your machines. You can track things like:
- Fuel consumption: Spotting unusual spikes can indicate engine problems or inefficient operation.
- Idle time: Excessive idling wastes fuel and increases wear and tear.
- Operating hours: Helps you schedule maintenance based on actual usage.
- Location: GPS tracking technology enhances fleet visibility, helps in theft detection, and reduces downtime at job sites.
This data is usually accessible through a web portal or mobile app, giving you real-time insights into your entire fleet. It's like having a mechanic constantly checking under the hood, but from a distance.
Predictive Maintenance Tools
Predictive maintenance takes data tracking a step further. Instead of just reacting to problems, it uses data analysis to anticipate them. These tools look for patterns and anomalies that might indicate an impending failure. For example, a gradual increase in engine temperature over time could signal a cooling system issue before it causes a breakdown.
By identifying potential problems early, you can schedule maintenance proactively, minimizing downtime and preventing costly repairs. It's about shifting from reactive maintenance to a more strategic, preventative approach.
Remote Monitoring Solutions
Remote monitoring solutions allow you to keep an eye on your equipment even when you're not on-site. This is especially useful for equipment operating in remote locations or on large job sites. These systems often use sensors and cameras to provide real-time visual and performance data. You can check on equipment status, monitor operating conditions, and even receive alerts if something goes wrong. It's like having a virtual presence on the job site, ensuring your equipment is running smoothly and safely. Keeping track of important data can help you fix issues more effectively, which in turn can help extend your equipment's life.
Creating a Safe Work Environment
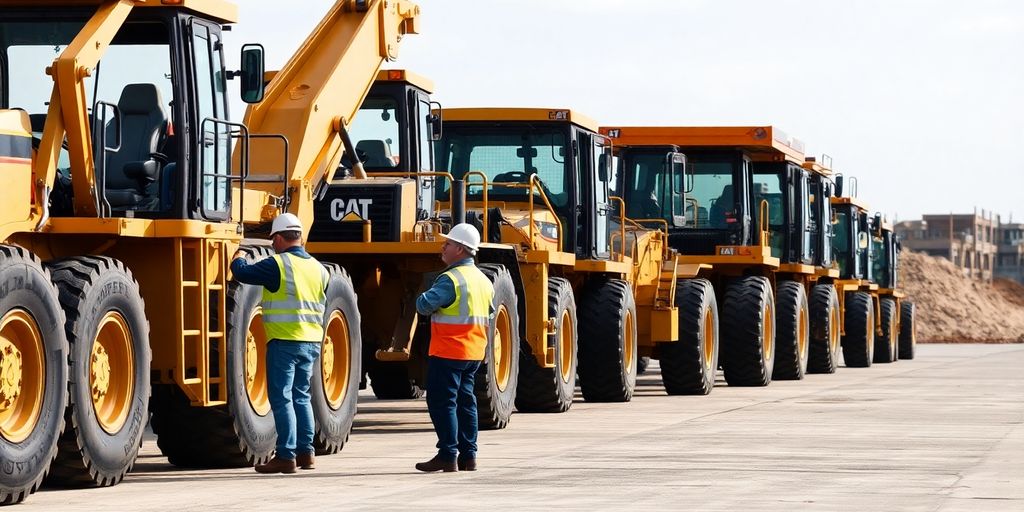
It's easy to overlook safety when you're focused on deadlines and keeping things moving, but a safe work environment is absolutely essential. It's not just about avoiding accidents; it's about creating a culture where everyone feels valued and protected. When people feel safe, they're more productive, engaged, and less likely to make mistakes. Plus, a strong safety record can save a company money in the long run by reducing insurance costs and preventing costly downtime due to accidents.
Safety Protocols for Equipment Use
Having clear, well-defined safety protocols is the first step. These protocols should cover everything from pre-operation checks to emergency shutdown procedures. Make sure these protocols are easily accessible and that everyone understands them. It's also a good idea to have regular refresher courses to keep the information fresh in everyone's minds. Here are some key areas to cover:
- Equipment-specific procedures: Each piece of equipment should have its own set of safety guidelines.
- Personal Protective Equipment (PPE): Clearly define what PPE is required for each task.
- Communication protocols: Establish clear communication methods for reporting hazards and emergencies.
Identifying and Mitigating Hazards
It's important to proactively identify potential hazards before they cause problems. Regular site inspections are a must. Encourage workers to report any potential hazards they spot. Once a hazard is identified, it needs to be addressed quickly. This might involve fixing a broken piece of equipment, improving lighting, or implementing new safety procedures. Regular equipment inspections are key to spotting issues early.
A good way to think about hazard mitigation is to use the hierarchy of controls: eliminate the hazard if possible, substitute it with something less dangerous, use engineering controls to isolate the hazard, implement administrative controls like safety procedures, and finally, use personal protective equipment as a last line of defense.
Regular Safety Training Sessions
Training isn't a one-time thing; it needs to be ongoing. Regular safety training sessions are crucial for keeping everyone up-to-date on the latest safety procedures and best practices. These sessions should be interactive and engaging, not just a boring lecture. Consider using simulations or real-life scenarios to make the training more effective. Make sure to cover topics like basic operations and malfunction identification. Here are some ideas for training topics:
- Emergency response procedures
- Hazard communication
- Safe lifting techniques
Investing in Quality Parts and Repairs
It's tempting to cut corners when equipment breaks down, but skimping on parts and repairs can lead to bigger problems down the road. Think of it like this: a cheap fix might get you running again today, but it could cause a major breakdown next week. That's why investing in quality is so important.
Choosing OEM vs Aftermarket Parts
Okay, so you need a new part. Now comes the big question: do you go with an OEM (Original Equipment Manufacturer) part or an aftermarket part? OEM parts are made by the same company that made your equipment. They're designed to fit perfectly and perform exactly like the original. Aftermarket parts, on the other hand, are made by third-party companies. They can be cheaper, but the quality can vary a lot. Choosing the right part is a balance of cost and reliability.
Here's a quick rundown:
- OEM Parts: Higher cost, guaranteed fit, reliable performance, usually come with a warranty.
- Aftermarket Parts: Lower cost, fit can be questionable, performance varies, warranty might be limited or nonexistent.
Consider the long-term impact. Sometimes, spending a little more upfront on OEM parts saves you money in the long run by preventing future breakdowns and extending the life of your equipment.
Importance of Professional Repairs
Just like using the right parts, getting professional repairs is key. Sure, you might be able to fix some things yourself, but complex repairs are best left to the experts. A certified technician has the training, experience, and tools to diagnose problems accurately and fix them correctly.
Trying to fix something yourself without the proper knowledge can actually make the problem worse. You could damage other components or even create a safety hazard. Professional repairs ensure the job is done right, keeping your equipment running smoothly and safely.
Cost-Benefit Analysis of Quality Parts
Let's talk numbers. It's easy to see the immediate cost savings of using cheaper parts or delaying maintenance. But what about the long-term costs? Think about downtime, lost productivity, and the potential for major repairs down the road. A proper cost-benefit analysis can help you see the bigger picture. Consider these factors:
- Initial Cost: The price of the part or repair.
- Lifespan: How long the part is expected to last.
- Downtime Costs: The cost of lost productivity while the equipment is out of service.
- Potential for Further Damage: The risk of using a lower-quality part or delaying repairs.
By weighing these factors, you can make informed decisions about equipment maintenance and repairs that will save you money and extend the life of your heavy equipment fleet.
Optimizing Equipment Usage and Load Management
Understanding Load Limits
It's easy to push equipment, especially when deadlines loom. But ignoring load limits is a surefire way to shorten its lifespan. Always refer to the manufacturer's specifications for maximum load capacities. Overloading leads to increased stress on components like hydraulics, engines, and transmissions. This can cause premature wear and costly breakdowns. Think of it like this: consistently lifting more than you should will eventually break something. It's not a matter of if, but when. Understanding transporting heavy equipment is crucial for maintaining equipment integrity.
Minimizing Idle Time
Idling might seem harmless, but it's a silent killer for heavy equipment. Excessive idling wastes fuel and causes unnecessary engine wear. It can also lead to issues like cylinder glazing, where the cylinder walls become too smooth for proper lubrication.
Here are a few ways to cut down on idle time:
- Implement a strict no-idle policy.
- Use automatic engine shutdown systems.
- Train operators to shut down equipment when not in use for more than a few minutes.
Minimizing idle time is not just about saving fuel; it's about extending the life of your engine and reducing overall maintenance costs. It's a simple change that can have a big impact.
Balancing Equipment Utilization
Spreading the workload across your fleet is key to preventing overuse of individual machines. If you have multiple pieces of equipment capable of performing the same task, rotate their usage. This ensures that no single machine bears the brunt of the work. Track equipment hours and maintenance schedules to identify potential imbalances. Consider factors like terrain, operator skill, and specific job requirements when assigning equipment. A well-balanced fleet is a happy fleet, and a happy fleet lasts longer. It's also important to avoid too much idling to prevent engine wear.
Wrapping It Up
In the end, taking care of your heavy equipment is all about being proactive. Regular maintenance, proper training, and daily checks can really make a difference. It’s not just about fixing things when they break; it’s about preventing those breakdowns in the first place. By keeping an eye on your machines and treating them right, you can save money and keep your projects running smoothly. So, whether you’re managing a big fleet or just a couple of machines, remember that a little effort goes a long way in extending their life. Trust me, your wallet will thank you later.
Frequently Asked Questions
What affects the lifespan of heavy equipment?
The lifespan of heavy equipment can be influenced by several factors, including how often it's used, the type of work it's doing, the quality of maintenance it receives, and the environment in which it's operated.
How long can I expect my heavy equipment to last?
On average, heavy equipment can last between 10 to 15 years. However, this can vary based on maintenance and usage.
What are some signs that my equipment is aging?
Signs that your equipment is aging include unusual noises, decreased performance, frequent breakdowns, and visible wear and tear.
Why is regular maintenance important for heavy equipment?
Regular maintenance helps prevent unexpected breakdowns, keeps the equipment running efficiently, and can save money on repairs in the long run.
How can I train my operators effectively?
You can train your operators by providing comprehensive training programs that cover proper equipment use, safety procedures, and how to spot potential issues.
What is telematics and how does it help with equipment monitoring?
Telematics is a technology that allows you to track your equipment's location, usage, and performance data remotely. This helps you monitor its condition and schedule maintenance when needed.