How to Plan Your Fleet for Multi-Phase Construction Projects
.png)
lanning out your equipment for big construction jobs, especially ones with different stages, can be a real headache. You need certain machines for digging, others for building, and then totally different ones for finishing up. If you don't plan this right, you can end up with machines just sitting around, costing you money, or worse, not having what you need when you need it. This guide will walk you through how to get your fleet sorted for multi-stage projects, so things run smoothly and you save some cash.
Key Takeaways
- Figure out what equipment each project phase needs.
- Plan for smooth changes between different project stages.
- Look into flexible rental options for your equipment.
- Find ways to use your machines better and save money.
- Use tech tools to help manage your equipment.
Strategic Fleet Planning For Multi-Phase Projects
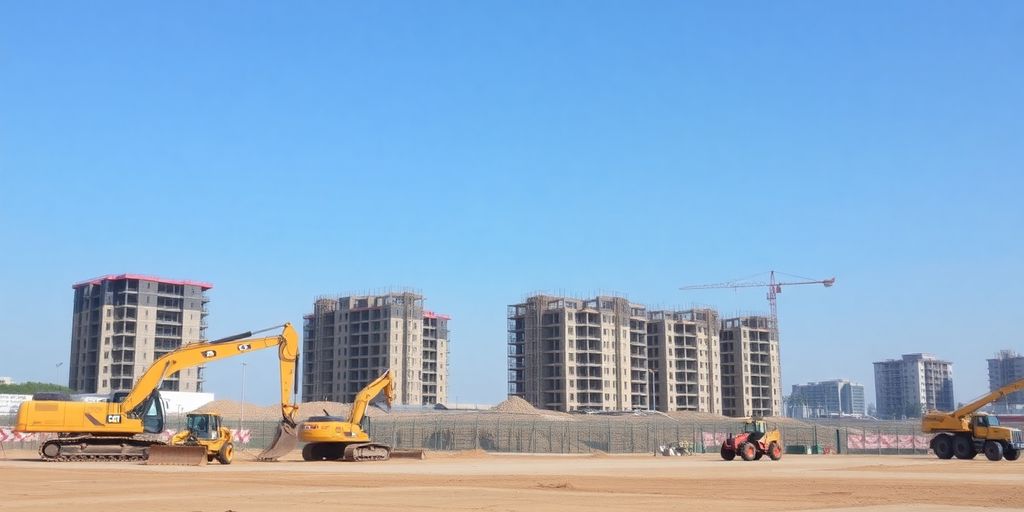
Multi-phase construction projects present unique challenges when it comes to fleet management. It's not enough to simply acquire a bunch of equipment at the start and hope it all works out. A well-thought-out strategy is essential for maximizing efficiency and minimizing costs. Let's explore how to approach this.
Understanding Project Phases
Each phase of a construction project—from initial site preparation to final finishing—demands different types of equipment. For example, the equipment needed for accurate estimates during site clearing is vastly different from the tools required for interior fit-out. Recognizing these distinct needs is the first step in effective fleet planning. Consider these points:
- Site Preparation: Bulldozers, excavators, and graders.
- Foundation Work: Concrete mixers, cranes, and pile drivers.
- Structural Erection: Tower cranes, welding machines, and steel erectors.
- Finishing: Scissor lifts, paint sprayers, and flooring equipment.
Benefits of Phased Fleet Allocation
Allocating your fleet based on project phases offers several advantages. Instead of having all equipment on-site from day one, you can bring in specific machines only when they're needed. This approach reduces idle time, lowers fuel consumption, and minimizes wear and tear. Here's a quick rundown:
- Reduced equipment rental costs by only hiring when needed.
- Lower fuel consumption due to less idle time.
- Minimized wear and tear, extending equipment lifespan.
Phased fleet allocation allows for better budget control and resource management. By aligning equipment needs with project milestones, you can avoid unnecessary expenses and ensure that the right tools are available at the right time.
Avoiding Common Pitfalls
Poor planning can lead to several problems, including equipment shortages, delays, and cost overruns. One common mistake is underestimating the time required for equipment transitions between phases. Another is failing to account for potential scope changes. To avoid these pitfalls, consider the following:
- Conduct thorough site assessments to identify potential challenges.
- Develop a detailed equipment schedule that aligns with project milestones.
- Establish clear communication channels between project managers and equipment suppliers.
Matching Fleet Requirements To Each Project Phase
Each phase of a construction project demands a specific set of tools and machinery. It's not a one-size-fits-all situation. What you need for breaking ground is totally different from what you'll use for the finishing touches. Smart planning means aligning your fleet with these changing needs to avoid wasted resources and keep things moving smoothly.
Equipment For Site Preparation
Site preparation is all about getting the area ready for the real work. Think clearing land, moving earth, and setting up access routes. For this, you'll typically need:
- Skid Steers: These are great for moving materials and clearing debris.
- Tipper Trucks: Essential for hauling away dirt and bringing in supplies.
- Water Carts: Keeping dust down is crucial, and water carts do the job.
These machines help you prep the site efficiently, ensuring a safe and workable environment. Don't forget about proper construction crew scheduling software to keep everyone aligned.
Machinery For Foundations And Structural Work
Once the site is prepped, it's time to lay the foundations and build the structure. This phase requires heavier, more specialized equipment:
- Excavators: Digging foundations and trenches is their bread and butter.
- Loaders: Moving large quantities of materials like gravel and concrete.
- Telehandlers: Lifting and placing materials at height, offering great reach and versatility.
Having the right heavy machinery is key to keeping this phase on track. Delays here can have a ripple effect on the entire project.
Tools For Finishing And Fit-Out
The final phase is all about the details – the interior work, the finishes, and the final touches. The equipment needed shifts again:
- Scissor Lifts: Perfect for reaching ceilings and walls for painting and installation.
- Light Vehicles: For transporting workers and materials around the site quickly.
- Smaller Power Tools: Drills, saws, and other hand-held tools for detailed work.
It's easy to overlook the importance of this phase, but having the right tools ensures a high-quality finish and a satisfied client. Don't underestimate the impact of efficient fit-out on the overall project success.
Managing Overlaps And Equipment Transitions Seamlessly
Multi-phase construction projects are like a relay race; you've got to pass the baton smoothly. When one phase ends and another begins, there's often a tricky period of overlap. This is where things can get messy with equipment. You might have machines sitting idle, costing you money, or worse, different teams fighting over the same equipment. It's a headache, but with some planning, you can make these transitions much easier.
Common Transition Challenges
Think about it: the demolition crew is wrapping up, but the foundation guys are already itching to start. That means you might have excavators and bulldozers sitting next to concrete mixers and steel reinforcement equipment, all vying for space. Here are some typical problems:
- Equipment arrives on-site way before it's actually needed.
- You've got multiple machines trying to do the same job, leading to wasted time and resources.
- Deliveries are late, throwing off the whole schedule.
- No clear communication about who needs what, when.
Strategies For Smooth Handovers
The key is communication and a solid plan. You need to know exactly when each phase starts and ends, and what equipment is needed for each. Here's how to make it happen:
- Detailed Scheduling: Create a super-detailed schedule that outlines when each piece of equipment is needed, and for how long. Share this with everyone involved.
- Regular Check-ins: Hold regular meetings with all the project managers and team leads to discuss progress and any potential roadblocks. This helps catch problems before they become crises.
- Staggered Deliveries: Don't have everything delivered at once. Coordinate deliveries so that equipment arrives just in time for when it's needed.
- Designated Staging Areas: Set up specific areas on the site where equipment can be stored temporarily. This keeps things organized and prevents congestion.
Having a buffer zone in your schedule can be a lifesaver. It gives you some wiggle room in case things don't go exactly as planned. This is especially important during transitions, where delays are common.
Minimizing Downtime Between Stages
Downtime is a killer. Every minute a machine sits idle, you're losing money. Here's how to keep things moving:
- Flexible Hire Agreements: Work with your rental company to get flexible agreements that allow you to return equipment early if you finish a phase ahead of schedule.
- Short-Term Rentals: Use short-term rentals to bridge the gap between phases. For example, if you need a small excavator for a few days to do some cleanup, rent one instead of keeping a larger machine on-site.
- Proactive Maintenance: Make sure all equipment is properly maintained to prevent breakdowns. Schedule regular maintenance checks and address any issues immediately.
- Operator Training: Ensure that all operators are properly trained and certified to use the equipment. This reduces the risk of accidents and delays.
Flexible Hire Solutions That Scale With Your Build
Project plans? They change. It's just a fact of construction. You might start thinking you need one thing, and then BAM, the scope shifts. That's why having hire options that can move with you is super important. You don't want to be stuck paying for equipment you aren't even using anymore!
Adapting To Scope Changes
The ability to adjust your equipment rentals as the project evolves is key. Think about it: site prep needs are way different from finishing work. If you're locked into long-term contracts for everything from day one, you're probably wasting money. Being able to scale up or down, swap out machines, or even just change the rental period can save a ton.
Short-Term Bridging Hire Options
Sometimes you just need something for a little while. Maybe there's a gap between phases, or a specific task that only takes a week. That's where short-term hires come in. Things like skid steers or water carts can be perfect for bridging those gaps without committing to a long rental. It's all about having the right tool for the job, exactly when you need it.
Rapid Swap-Outs And Adjustments
Imagine this: you're moving from foundation work to structural steel, and the excavator you've been using is now overkill. You need a crane, stat! A good hire company will let you swap out equipment quickly and easily, without a ton of red tape. This keeps your project moving and avoids downtime. It's about flexibility and responsiveness, plain and simple.
Having a hire company that understands the dynamic nature of construction projects is a game-changer. It's not just about renting equipment; it's about having a partner who can adapt to the inevitable changes and keep your project on track.
Optimizing Fleet Utilization And Cost Efficiency
It's no secret that construction projects can be expensive, and a huge chunk of that cost comes from the fleet. Getting the most out of your equipment while keeping costs down is a balancing act, but it's totally achievable with the right strategies. The goal is to ensure every piece of equipment is working efficiently and contributing to the project's progress.
Reducing Idle Machine Time
Idle equipment is basically money sitting still. Think about it: you're paying for the machine, the operator (if applicable), and the space it occupies, but it's not doing anything. Here's how to cut down on idle time:
- Scheduling is key: Plan your equipment needs carefully for each phase. Don't have a bulldozer sitting around waiting for the foundation to be poured. Use future fleet analysis to predict needs.
- Communication is also key: Make sure everyone on site knows the schedule and what equipment is needed when. Clear communication prevents delays and ensures equipment is ready when it's supposed to be.
- Maintenance matters: Regular maintenance keeps equipment running smoothly. A breakdown can cause significant delays and idle time for other machines waiting on the broken one.
Controlling Overlapping Hire Costs
Hiring equipment can be a great way to supplement your existing fleet, but it's easy to overspend if you're not careful. Overlapping hire periods, where you're paying for equipment you're not actively using, can quickly eat into your budget.
- Staggered rentals: Try to schedule rentals so that they start and end when you actually need the equipment. Avoid renting equipment too early or keeping it longer than necessary.
- Negotiate rates: Don't be afraid to negotiate rental rates with suppliers. You might be able to get a better deal, especially if you're renting multiple pieces of equipment or for a longer period.
- Return promptly: As soon as you're done with a piece of rented equipment, return it. Even a few extra days can add up to a significant cost.
Maximizing Return On Investment
Ultimately, the goal is to get the best possible return on your fleet investment. This means making smart decisions about what equipment to buy, what to rent, and how to use it efficiently. Careful planning is essential.
- Track utilization: Monitor how often each piece of equipment is being used. This will help you identify underutilized assets that could be sold or rented out.
- Consider lifecycle costs: When buying equipment, don't just focus on the initial purchase price. Consider the total cost of ownership, including maintenance, repairs, and fuel.
- Invest in training: Properly trained operators can use equipment more efficiently and safely, reducing wear and tear and minimizing downtime.
By focusing on reducing idle time, controlling hire costs, and maximizing return on investment, you can significantly improve the cost efficiency of your fleet and boost your project's bottom line. It's about working smarter, not harder, and making informed decisions based on data and careful planning.
Leveraging Technology For Enhanced Fleet Management
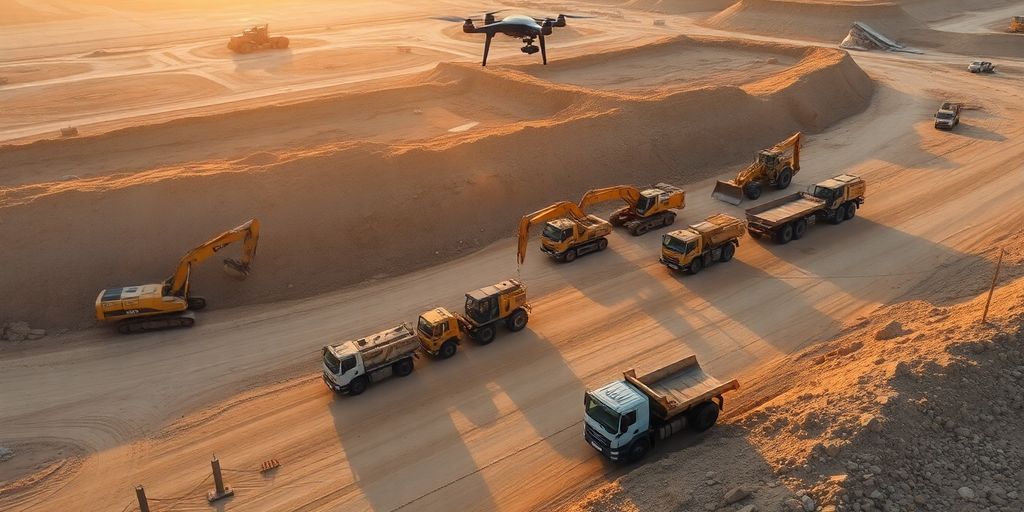
Technology is changing how we handle construction fleets. It's not just about knowing where your equipment is anymore; it's about using data to make smarter choices and run things more efficiently. I remember when keeping track of everything was a headache, but now, there are tools that can really make a difference.
Utilizing Integrated Solutions
Integrated solutions are the way to go. Instead of using different systems that don't talk to each other, you can have one platform that connects everything. This means you can see your entire fleet, track maintenance schedules, and manage costs all in one place. It's like having a command center for your equipment.
Data-Driven Decision Making
Data is king. With the right tools, you can collect tons of data about how your fleet is being used. This data can help you:
- Figure out which equipment is being underutilized.
- Spot potential maintenance issues before they become big problems.
- Optimize your fleet size for each project phase.
Using data to make decisions is no longer a luxury; it's a necessity. It helps you avoid guesswork and make informed choices that can save you money and time.
Real-Time Tracking And Monitoring
Real-time tracking is a game-changer. You can see where your equipment is at any given moment, which helps with security and logistics. Monitoring also lets you track how equipment is being used, so you can identify inefficiencies and make sure everything is running smoothly. For example, you can see if a machine is idling too much or if it's being used in a way that's causing unnecessary wear and tear.
Ensuring Safety And Compliance Across All Phases
Construction projects, especially multi-phase ones, are inherently risky. It's not just about getting the job done; it's about getting it done safely and within the rules. This means thinking about safety and compliance from day one and keeping it top of mind throughout every stage of the project. It's easy to let things slip when you're juggling multiple deadlines and equipment transitions, but that's when accidents happen.
Adhering To Safety Regulations
Staying on top of safety regulations can feel like a moving target. Regulations change, and they can vary depending on where you're working. The key is to have a system for staying informed and making sure everyone on site knows the rules. This might involve:
- Regularly checking for updates from regulatory bodies.
- Conducting site-specific risk assessments before each phase.
- Holding regular safety briefings to discuss potential hazards and safe work practices.
It's easy to think of safety as just a checklist, but it's really about creating a culture where everyone feels responsible for looking out for themselves and each other. When people feel empowered to speak up about potential hazards, you're much more likely to prevent accidents.
Regular Equipment Maintenance
Equipment failure is a major cause of accidents on construction sites. A poorly maintained machine isn't just inefficient; it's a hazard waiting to happen. Regular maintenance is non-negotiable. This includes:
- Following the manufacturer's recommended maintenance schedule for each piece of equipment.
- Conducting daily inspections to identify any potential problems before they become serious.
- Keeping detailed records of all maintenance activities.
Operator Training And Certification
Even the best equipment is only as safe as the person operating it. Make sure everyone who uses a piece of machinery is properly trained and certified. This isn't just about ticking a box; it's about giving people the skills and knowledge they need to operate equipment safely and effectively. Consider these points:
- Providing initial training for all new operators.
- Offering refresher courses to keep skills sharp.
- Verifying certifications are current and valid.
- Documenting all training activities.
Conclusion: One Hire Plan. Every Project Stage.
So, getting your equipment hire plan right isn't just about saving money. It helps keep your project on track, makes your work site run better, and keeps your crew moving at every step. Thinking ahead about what gear you'll need for each part of the job, and having a good plan for when things change, can make a big difference. It means less waiting around, less wasted cash, and a smoother build overall. It's all about being smart with your resources from start to finish.
Frequently Asked Questions
What does 'strategic fleet planning' really mean for big projects?
Effective fleet planning means looking at each step of your construction project (like preparing the site, building the main structure, and finishing up) and making sure you have the right machines for each part. This helps avoid wasted time and money.
Can I change my equipment rental if my project plans shift?
Absolutely! We focus on making sure you get the exact equipment you need, right when you need it. If your project plans change, we can quickly adjust your rental agreement, swap out machines, or change delivery times without a fuss.
Do you offer services for projects in remote areas?
Yes, we regularly deliver equipment to both big cities and far-off sites. Our machines are built to handle tough and changing conditions, so we can help you no matter where your project is.
What types of equipment are best for overlapping project stages?
For times when different project steps overlap, it's smart to use short-term rentals. Things like small loaders, water trucks, and light vehicles are great for filling gaps and keeping the work flowing smoothly.
How do you help reduce idle time between different project phases?
We work closely with your on-site team to make sure equipment swaps are smooth. We offer flexible change-outs and short-term rentals to help you move from one project stage to the next without delays.
How does technology help manage the fleet better?
We use smart tools and data to help you keep track of your equipment in real-time. This means you can see where your machines are, how they're being used, and make quick decisions to keep everything running efficiently.